It’s pretty safe to say that our sewing machines are by far the hardest working tool in our workspace but what about the little gadgets? These little guys can improve our sewing experience, shave down our cutting time and ultimately make us look like ROCK STARS! Here are my top 10 must have sewing tools for your studio.
My Must Have Sewing Tools
1. Flexible Tape Measure
Measuring an uneven or curved surface can be tricky but these flexible tape measures sure to make it easy.

2. Scissors
From fabric sheers to a smaller precision pair, these blades will come in handy! Sometimes, I even wear those mini blue ones around my neck as I sew. This way, I never misplace them.
3. Straight Pins
These little thin lines of metal are a must have in the sewing basket. While I personally like to use them sparingly, they are mission critical for matching points and seams.

4. Rotary Cutter
Talk about the best invention ever!! This little round blade of goodness can speed you through the fabric cutting stage and get you stitching on the machine in no time flat. I swear, I have them in every size & a pinking version.
5. Cutting Mat
This self healing mat is a MUST have when using the rotary cutter mentioned above. However, not all mats are created equal. Not only do the lines matter on this tool but so does the size.
Foldable Cutting Mat- When buying a large mat you also need to think about storage. That is why I love the foldable cutting mats.
Rotating Cutting Mat- Mind Blown! For all those quilters out there this mat will change your life. No more worrying about fabric shifting or having to move your fabric again. Total game changer!
6. Iron
I’m not going to lie, this is one tool that I struggle with. I’m not sure why but my irons seem to burn out every two to three years. That said, I have two top picks with side notes.
Oliso Pro- I just love the smart feet technology but word to the wise, I wouldnot recommend filling it with water and using it as a steamer. After a few years of hard work, it started to leak on me. Now, don’t get me wrong, I still use it everyday just without water!
Steamfast Travel Steam Iron- This little guy is on my must buy list. I have heard such amazing things about it and think it would be perfect right next to my sewing machine for heavy piecing days.
Panasonic Cordless- Some say that cordless is the way to go and this cutie has good overall reviews. I just wonder if the reservoir holds enough water to last me an entire pressing session.
No matter which iron you select, be sure that it will quickly become one of the hardest working tools in your space.

7. Soak Flatting Spray
Between the amazing smell and the magical results, this is spray is always within reach of my ironing board.
8. Heat Erasing Pen
It’s no secret that I like to doodle and with the help of these heat erasing pen I can draw worry free. *Tip: just be sure to spot test on each fabric before going hog wild.
9. Specialty Needles
Never has having the right tool for the job been more important then with sewing machine needles. Speciality needles can allow your machine to glide through fabric without tearing or nicking (ballpoint for knits), produce crisp and clean thick stitches (topstitching/denim), create two stitch lines in one pass (twin needle), and machine specific needles (serger).

10. Seam Ripper
And last but not least, no seamstress would be without their trusty seam ripper. Let’s be fair, this is the one tool that we despise using but it can get us out of a jam pretty quick. Make sure your seam ripper fits comfortably in your hand and is not too small. Also, did you know that little red ball at the end actually has a purpose?
credit: thesewingloftblog.com
Sewing Needles

The small number of seams in this pattern was a key factor. I did not sew up the waist tucks because the blouse would have lost the loose and airy look. Since the scenic-print fabric was really a scarf, there was some shortage; so I added a contrast silk chiffon yoke, adding a degree of time consumption. I reduced the original back button opening to a seam. TIP: Cut the chiffon with paper underneath to prevent it from moving around on you.

Sewing Needles & thread: For basting I used an embroidery sewing needle which has a large eye but is long and thin, and for permanent sewing I used a short, sharp needle, also a thin variety and just one inch in length. I used a contrast silk thread for basting and a fine polyester thread for permanent sewing with the short sharp sewing needle. TIP: your fabric should dictate the kind and size of sewing needle & thread. Serious hand sewers like to use a thimble, but I can safely say that it is optional.

Beeswax: Run the thread through the beeswax, iron the thread so that the wax is incorporated in the thread and will not come off on the fabric.
Putting it together: Stay-stitch neck edge of front and the two back pieces by machine. Stay-stitching and finishing the neckline was the only time I used the sewing machine.
Mark: Seam lines lightly with chalk, and the dot under the arm with a tailor’s tack. Thread-trace all seam lines, or you can follow the chalk lines (see why I used a pattern with few seams?).

Join the pieces at the yoke seam on the front and backs with a French seam. Here’s how: thread-trace or chalk-trace the 5/8 inch seamline only on one piece. Wrong sides together sew a 1/4” seam using a combination running and backstitch (first picture below). This means that after every three running stitches (1/8” each) you take a back-stitch. Trim the seam by a smidgen. Press open, then press together on the seamline, right sides together. Sew with the running-stitch/back-stitch on the thread traced line. See the orange basting thread in the picture? That was my guide, as seen in second picture below. You can also see the running/back-stitch in action. Remove orange basting! TIP: don’t sweat the small stuff. If your hand stitching is uneven, your garment will still be great!

Next, sew the center back in a straight seam with a running stitch/back-stitch combo, press open and “fell” the allowances; the center back is left open on the black upper yoke portion so the blouse can go over my head. The shoulder and side seams are stitched, and the seams are felled to one side without pressing open (that is how my elderly relative did the original tunic).
Apply binding to the neckline. Are you missing the sewing machine? I am, so the neck binding is applied on a machine. Turn in the sleeve hems and sew down with a slip stitch. My scarf/fabric was already hemmed at the bottom so I did not have to hem it – another concession to machine sewing! Voila! I thank my sewing needles and add the hand-made light & airy top to my wardrobe.
Today I'm really excited to share a no-sew refashion with you. You might get a little messy but it will be a lot of fun in the process. All you need is a dress and a few basic supplies. Of course if you want to change the fit of your dress, you'll need to do a little stitching but otherwise you don't need a sewing machine at all. So, get your rubber gloves on and read on to see how I transformed this dress from drab to fab.

I bought this bright purple 80s-era dress way back in 2009. I did a partial refashion removing the sleeves and an extra layer of fabric that covered the bodice. (Yes, sewing was required for that part. :) I didn't think I'd wear the purple color very often, so I attempted to dye it navy. I used acid dyes that I thought would work on the synthetic material but the dye only took in a few spots, namely, the underarms and some areas on the skirt. (The horror!) I really didn't want to wear a dress with black pit stains so I tossed it in the closet and only thought of it once every year or so when I went to clean out the closet. I really couldn't tell you now why I thought I should keep it but I guess I figured that it had good bones and one day I'd eventually figure out how to make it wearable.

Then last week, I was invited to a party and instructed to wear purple. The only purple thing I could find in my closet was a slightly ratty t-shirt and that would not do for a party. Then I remembered this dress, so I dug it out of the closet and set to work. I recently dyed some old leather bags using leather dye and the leather dye stained my rubber gloves so I thought it would probably work on this dress. I know, I know, I'm not using it as advised but I did a little test and it worked! If your dress takes dye better then by all means use a dye intended for fabric. The other change was I added suede epaulette-like patches to the shoulders. I think it gives it a cool futuristic kind of edge.

Painted Dress No-Sew Refashion
Supplies:
Black Leather Dye (or dye of your choice)
Suede Elbow Patches (the pack comes with two put you only need one)
Permanent Double Stick Fusible (such as Steam-a-Seam)
Rotary Cutter and Self-Healing Mat or Scissors
Iron
Synthrapol soap and/or white vinegar
Instructions:
Step 1: Paint your dress. Cover your surface and wear rubber gloves to keep from getting dye everywhere. I used the little dauber that came with the leather dye to create very soft brush strokes and dots, randomly sprinkled all over the dress. Don't worry too much about making it perfect. Hang up the dress and let it dry. (If you do get dye on your hands, try scrubbing them with baking soda and water.)
Step 2: Wash the dress in Synthrapol soap and/or vinegar to discharge any extra dye. Rinse until dye no longer discharges from the dress. Allow the dress to dry.

Step 3: Add suede patches to the shoulders. Using your rotary cutter, cut one suede patch in half. Trace 2 half circle shapes onto a sheet of double stick fusible and cut out. Peel off one side of the fusible and stick to the wrong side of each patch. Trim any excess double stick.
Step 4: Remove remaining paper from fusible and, with the straight side of the patch aligned to the top of the armhole, adhere patch to shoulder. Check placement and reposition if needed. Using a press cloth, iron the patch to permanently bond it to the dress. To be safe, iron both sides.

So, what do you think? Will you try painting your clothes? If you're looking for more inspiration, check out my Brushstroke Moodboard and my Painted Stripe Dress.
credit: sewdiy.com
Seam
rippers are standard issue with sewing machine these days but most of
us only think to use them at that UGGHHH moment. You know the one, when
you are in a rush and something happens that makes you want to pull
your hair out!
Well, today Carolina turns it all around and
shows us just the opposite. Love it!! So, let’s give a warm welcome to
Carolina from Always Expect Moore and get stitching.
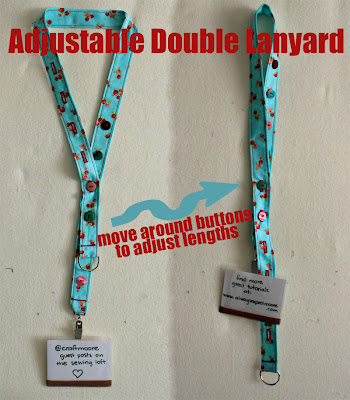
I’m
so excited to be guest posting here at The Sewing Loft today! I first
started sewing when I was about 7 years old, on a My Little Pony chain
stitch machine. When I was 13 I went to quilt camp. At 16 I took garment
sewing lessons. Even though my mother is an amazing seamstress, she let
me learn from others and waited patiently for me to come to her to ask
questions. In that way she fostered my love of sewing. Now, I blog about
crafting and sewing at Always Expect Moore and even teach sewing and
quilting classes at my local quilt shop!
When Heather told me
that she was looking for sewers to share tools, I knew I had to share
the seam ripper. The challenge was to come up with a project that
intentionally uses a seam ripper… though many of my projects
unintentionally use one!
First, I thought I would share with you some tips for the traditional way to use a seam ripper:
Now on to today’s tutorial! I go to conferences or other events where I need a name badge. Sometimes I want a second name badge to highlight my twitter handle or something about me, but don’t want to wear a second lanyard. Sometimes I only need one badge, but it is handy to have a loop where I can attach my keys to keep them handy, or clip a pen for easy access. This lanyard adjusts depending on what I need to use it for… and is super cute to boot!
What you’ll need is some fabric, coordinating buttons (I used 6 buttons that are all different, which is fine, but they should be roughly the same size), a lanyard clip or other fastener for one end and a large key ring for the other, and a turning tool (or safety-pin). Plus… have your seam ripper handy!
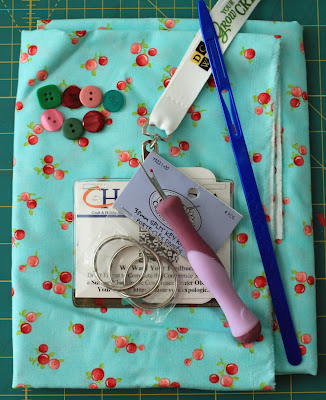
I started with a 3″ x WOF (that means “Width of Fabric”) strip, folded it in half, right sides together (RST), to make 1.5″ x WOF and stitched down the raw edge.
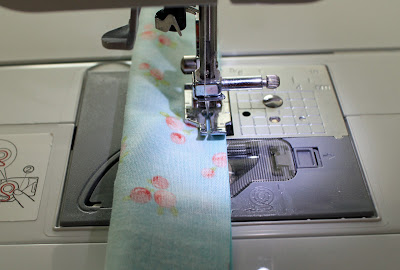
I used my turning tool to turn the tube right side out, and then pressed it flat with my iron.
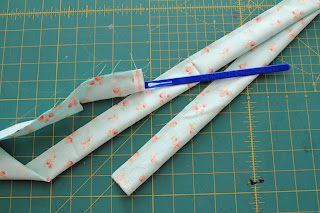
Using a contrasting thread, I stitched 1/8″ away from the edge on both sides.
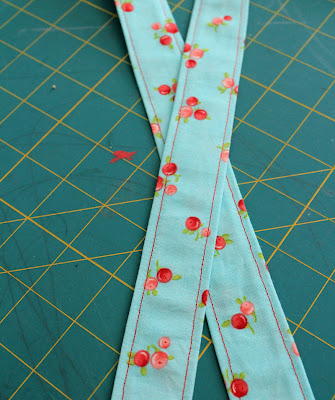
4″ from each end, I marked 6 dots, each 2″ apart.
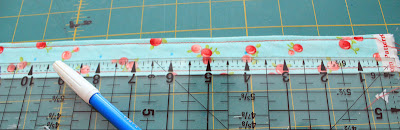
Using my buttonhole foot, I stitched a buttonhole at each dot on one end of the strip. If you have one of these buttonhole feet and don’t know how to use it, search YouTube for a tutorial on how to use it for your brand sewing machine – you’ll be glad you did. These are awesome!
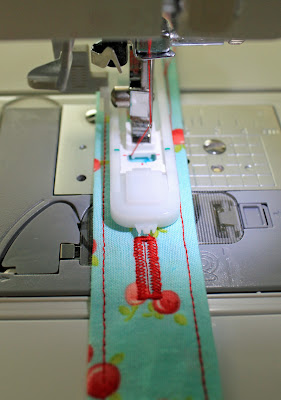
Here is where you get out your seam ripper. At one end of the buttonhole, put a pin perpendicular to your stitched hole. Insert your seam ripper at the other end, and carefully pull towards the pin. The pin will serve as a “stop” so that you don’t rip right through the other end of the buttonhole.
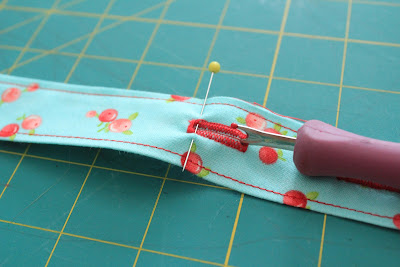
Once you’ve cut open all the buttonholes, stitch a button on each of the marks you made on the other end of your fabric strip.
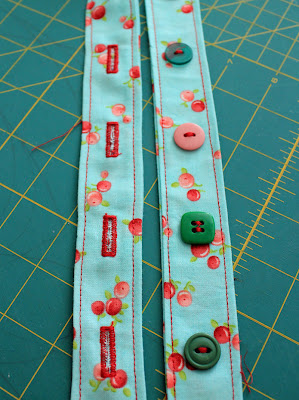
Trim off the raw ends of fabric, fold the end over twice, slip the hardware on each end, and pin in place. Stitch where you have pinned – I used a small zig-zag stitch.
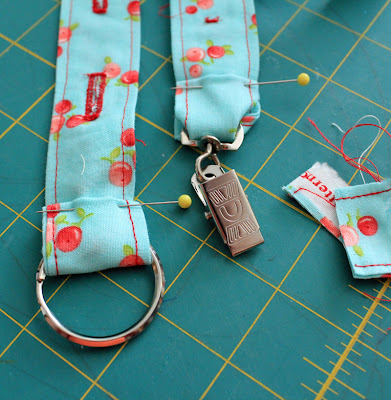
Once you’re done you can slip a couple of the buttons into buttonholes to adjust the two ends of your lanyard!
credit: thesewingloftblog.com/
With your Bias Tape Maker!
I am slightly embarrassed to admit it but I have not 1 but 3 bias tape makers in my sewing tool box that have never been used. So, when Jean told me about her favorite tool selection, I was all ears! It was like she knew they were tucked away just waiting to be used.
Hi there, I’m Jean Kake from the Quilted Cupcake blog, podcast and Etsy shop. One of my favorite things to create is handmade bags – I give them as gifts, use them myself, and sell them in my Etsy shop.
Here are a few of my recent bags:

Tutorial: Easy Bag Handles using Bias Tape Maker Tool
Creating handles for my bags was always a pain for me. Especially if I wanted a sturdy handle. I discovered an easy way make handles that are strong without having to deal with turning a fiddly tube of fabric.
My favorite method uses a bias tape maker tool, like this these from Clover. I use the biggest one for most of my handles – it’s #50 for 2 inch “tape”.
They’re designed to create bias binding for quilts, etc; however, they work really well to make long lengths of perfectly pressed lengths of fabric.
There are three secrets to using the bias maker tool:
Read the directions to see the SIZE of the fabric strip you need. Mark this number on your bias tape maker with a piece of tape or a fancy label, so you’ll remember each time you use it. Cut your fabric to that size to start. For the #50 tool, the strips should be 3 7/8″ wide.
You don’t need to cut the fabric on the bias when making handles this way. I usually just cut a strip the whole length of the fabric. Fold the fabric into a “point” when threading it through the wide end of the tool. Use a pin poked through the hole of top of the binder to guide the beginning edge of the fabric through the tool.

Once you’ve done these few things, the process for making the binding tape is super easy. Once you’ve threaded the end through, just hold onto the pop-up handle and pull the tool along to the left, while ironing from the right.
You’ll end up with a 2 inch wide handle that’s nicely pressed on each edge. Now, repeat the process with a second strip of fabric cut the same way. I chose a contrasting color, but you can use the same fabric if you like.
Stack them together, wrong sides (or folded sides) together, and stitch along each edge.
Ta-da – perfect bag handle – and you didn’t have to turn a tube.
To make the handle even sturdier, you can iron a 1.5 inch strip of fusible interfacing on one folded side prior to sewing the two halves together; however, I find that makes the handles too stiff.
Another option is to make one strip a heavier weight fabric – that’s what I did for the second handle shown. The owl print is a home-dec weight, adding additional durability to the handle.
Please feel free to send me any questions you may have on this technique. I always love meeting new crafters and quilters. I’d love for you to become a Facebook friend (Jean Kake), or like my Quilted Cupcake page: http://www.facebook.com/QuiltedCupcake
You can find all my Twitter/Pinterest, etc. links on my blog: www.quiltedcupcake.net, or email me at quiltedcupcake@gmail.com
Love it Jean!! You have inspired me to dig out my bias tape makers and make a quick strap. Stay tuned, Lindsay from Craft Buds is our special guest tomorrow.

Today I'm excited to share this easy, no-sew DIY tutorial, a knock-off of this scarf from Anthropologie. This scarf makes a great addition to your everyday spring wardrobe and a lovely gift for Mother's Day. All you need is fabric, dye and a paint brush. Oh, and a little bit of confidence painting. But trust me this is really easy to paint and super fun too.

As soon as I saw our inspiration scarf, I thought it would make a great DIY knock-off. I love the abstract, uneven texture and the exposed brushstroke look. This scarf is just 2 yards of fabric painted with dye. The ends are left raw and the selvages are intact. When you choose your fabric, make sure you like the look of the selvage. For this version, I used a very lightweight cotton voile that is 58 inches wide. It's BIG but the fabric is so thin it folds up quite nicely around the neck. I bought the fabric from Michael Levine downtown for just $5 a yard. I think this is it online. This DIY costs about $20 to make which is a great bargain compared to the original cost of our inspiration scarf.

DIY TUTORIAL: Brushstroke Painted Scarf
Supplies:
2 yards pink cotton voile
Dye-Na-Flow liquid dyes
Paintbrush
Scissors or Rotary Cutter
Instructions:
Step 1: Trim the raw ends of fabric and gently fray. Lay out fabric flat on a protected work surface.
Step 2: Mix blue, black and violet dye in glass jar. (You don't have to mix but I wanted my color to be darker and redder.) Dip brush into dye and tap off excess. Paint rough stripes the length of the fabric. Repeat until fabric is covered in stripes. Touch up as needed.
Step 3: Allow fabric to dry. Set dye by ironing. Touch up frayed ends as needed.

Some notes: I was intending to post this DIY last week as part of my brushstroke theme. I made a scarf using a white poly-cotton blend and I added water to the dye. The dye spread a lot during painting, soaking into the fabric. I even took pictures of the scarf but ultimately decided that I didn't love it.
I chose to use dye rather than paint because I wanted the color to soak into the fabric as opposed to sitting on top. After my first psuedo-fail, I even tried paint but didn't like it. It was much too heavy for the voile. So I went back to the dye, and by not adding water, it really was the perfect medium. I highly recommend testing out your painting on a fabric scrap before starting on your scarf.

What do you think? Will you make yourself a painted scarf this spring? Or maybe one for Mother's Day? I hope you enjoy the tutorial!
credit: sewdiy.com/